
Erie Powder Coatings NewsletterMarch 2017
Quality Control
To quote the article from our technical corner by Dan Magruder, “Everyone that sprays pow-der has a quality control program to one extent or another. “ Quality Control is an essential element of any manufacturing operation. And everyone is doing QC, whether they know it or not. A simple visual evaluation is simply, quality assurance, provided there is a consquence.
To be sure, some companies have much more developed and robust QC programs than others. Some are forced to follow certain QC standards by their customers, or their custom-ers customers. Others are simply finding these programs as best practice.
Any which way you look at this however, there are some best practices. I would point out a few important factors in a solid QC program, below:
- Quality Control Costs – There are costs to a QC program, but the benefits will out-weigh the costs. A single failure in the field due to lax QC can destroy a company.
- Training and auditing – as with any program, no matter how good the program is, without training employees on both the how and the why of QC and then auditing the results and implementation, QC will not be carried out the way your company needs to.
- Record it – QC can be easy or hard. It can be complex or as simple as a quick visual inspection. Any which way that it is done however, it needs, it is absolutely essential, that the results be recorded..
“Quality is do-ing the right thing when no one is looking.”
Henry Ford
In This Issue
- QC info
- SP289-T7 7035 Gray Text
- EPC News
- Technical Corner: focus on Quality Control
- Time at Tempera-ture, and curing
Product Showcase: SP289-T7 7035 Light Gray Text Superdurable
In this months showcase, we bring out another of our rolling texture RAL colors. This color is matched to RAL 7035, Light Gray.
We have brought another of our rolling textures to the showcase due to the popularity and success of these coatings in the powder market. Our sales people are consistently coming back to our lab and production people and telling them how much our customers are loving these products. Why? Consistency, which has always been a problem in the industry for these types of powders. This
particular product is a superdurable polyester TGIC.
Call us today if you would like more information on this product, or a sample.
Erie’s SP289-T7 7035 Light Gray Texture Superdurable— ask your sales rep or call our office
EPC News
Pricing info: Erie / EPC have not brought out a general pricing increase for the start of 2017, unlike
some of our competitors.
However, we would like to note some general info on the main ingredients in powder coating: polyester, epoxy and titanium dioxide. These three ingredients are by far the largest volume raw materials for most powder coating formulas. All three of these have been subject to pricing pressure and some significant pricing increases.
Titanium Dioxide: Titanium dioxide has already gone through, and continues to see, large increases in pricing. For information on titanium dioxide, a simple google of “chemours price increase” will give the reader lots of information. Chemours (formerly Dupont) is by far the world leader in market share, and because of the large market share, they lead the industry in any pricing changes. Chemours has just announced a third pricing increase in 12 months for Feb 2017 of about $150 / metric ton. In total, the pricing is up approximately 20% from a year earlier.
Polyester: Supply issues in China appear to be making problems for N America producers. Although Erie buys none of its polyester from China, supply disruptions in China will also have an effect in N America. Pricing on polyester has moved upwards in late 2016.
Epoxy: Epoxy also has been relatively steady in 2016, but we have been warned of pricing increases coming. These increases would be due to market supply and demand more than any other factor.
To summarize, titanium dioxide has been a very large price mover already in the last year. Epoxy and polyester both appear to have some pressure for pricing increases, some of which has already been implemented. Two of the largest pricing factors, currency exchange rates and duties importing into the American market, both remain a mystery at this time, with lots of potential changes coming.
Quality Control
Quality control can take many different forms and encompass every part of a process in a production facility.
While quality control equipment can be extremely expensive, both for purchase but also for maintenance, there are often other ways to improve quality without destroying your budget.
For example, simply adding sufficient light at the end of the production line for inspection can make all the difference in ensuring that finished product is looking good before it goes out the door. While lighting isn’t free by any means, this is a very low cost way of adding assurance to your quality program.
Last, we would emphasize, as we always do, recording of the results of the quality control, and also of any audits undertaken. Without this data, a coater will not be able to convince his customer that they are doing all they can to perform at a high quality level.
Additionally, having QC records to review at a later date are the only way to check that QC is completed regularly and the only way to evaluate whether changes are needed in the QC program.
Technical Corner
QUALITY CONTROL, SIMPLE STEPS TO AVOID COSTLY MISTAKES
Everyone that sprays powder has a quality control program to one extent or another. The simplest and probably most common, is a final visual inspection of a finished part. While this is effective to some extent, it’s a bit like closing the barn door after the cow gets out. Any part that fails, has to go through at least some of the process over again, or worse, must be rejected totally. There are of course, other, more sophisticated quality control programs that are very thorough and very extensive. Generally these tend to be used at OEM (Original Equipment Manufacturers) and other industrial finishers that have very specific, well defined parameters that quantify quality. There is very little room for opinion. The part passes, or it fails. In any event, ALL REJECTED PARTS CARRY A HEAVY COST.
A good quality control program, QCP, will not only define pass/fail criteria, it also addresses how the problem is to be rectified and where in the process stream this needs to take place. This serves a dual purpose of fixing the current problem and making changes to the system to avoid similar failures in the future.
My experience is that most powder coaters have a QCP somewhere in the middle. Generally this is sufficient to keep rejects low and maintain adequate output to main-tain profitability. I have found that the most successful coaters in the business em-ploy a sound QCP as part of their overall service package to their customers. One of the hardest things to overcome is that end user customer that cannot or will not de-fine the necessary parameters to quantify pass/fail for his finished parts. In most cases the coater is left to make this determination on his own.
I believe it is safe to say that any QCP is better than none at all. Additionally, the more stringent the program, the more clearly defined it is, the less likely rejected parts will cost the coater time and or money. I know of very few end customers that will accept and pay for parts that don’t meet their definition of quality. By working with your end customers to define quality parameters, whether they are end user “retail” customers, or they are co-workers somewhere in the production stream, you will be adding value to your product and your process.
As we look forward to 2017 take a minute or two to evaluate your QCP. Ask yourself, “Are there ways that I can increase the quality of our work and are there ways to further reduce rejects and re-work.”? Any incremental improvements that can be made will ultimately increase profit margins as well as enhancing your place as a true partner in your customers’ success.
The following are suggestions that may seem obvious but in each case, if they are not currently being used, the addition of these actions will enhance your overall quality program.
For liquid pre-treatment systems, be sure to check concentrations of chemicals a minimum of once a day, preferably once each shift.
For manual blasting and mechanical pre-treatment, check the media often. If your media is contaminated its use will also further contaminate parts.
Be sure you have a good ground in your spray booth. Poor grounding causes powder usage to go up and quality to go down. Clean hooks, carts, and booth parts as often as necessary.
Do a standard MEK rub test on finished parts at least once a day, preferably once a shift.
Have your oven tested every 6 months or a minimum of once a year. Undercured parts fail more quickly than parts that are cured correctly.
Always keep your powder in a cool, dry location away from heat sources and always keep the bag closed tightly and secured with a tie of some sort. Twisting the bag and folding it down in the box is not adequate.
Always keep guns, hoses and booths cleaned and replace wear parts as needed.
Be sure to check air-lines and air dryers at least daily, more often when the weather is very humid.
Dan Magruder
Sales Manger, Eastern US
Continuing Education— General info on powder coatings.
Continuing Education
Metal Temperature of Powder Coatings— What does this mean?
This I our ongoing series on educational information for coaters and users of powder coating.
On our technical data sheets, along with virtually all of our competitors, you will see a term something like “metal temp” when looking at cure times.
What does this mean, and why do all the manufacturers use it?
All thermoset powder coatings cure with heat. This is really the definition of the coating type. For example, it may take a spe-cific powder coating 15 minutes at 170C (340F) to fully cure. So why do powder coating manufactures qualify this curing tem-perature with the “metal temperature” statement?
The main issue is that there is a disconnect between oven (air) temperature and the temperature that the actual coating is see-ing.
Imagine two parts going through an oven. The oven is set at 400F. This means the parts should be at 400F correct? Not so at all, even if we make it a given that the oven (and sensors) are actually working perfectly well, and that the air temperature is actually 400F. If one part being sprayed is 2 inches thick steel, and the other part is 16 gage sheet metal, it seems obvious that the much thicker part will take much longer to get “up to temperature”. In fact, the thicker part may never even approach the air temperature at 400F, whereas the sheet metal will likely get very close to this air temperature, and in a fairly quick time.
Thus, in this case, the sheet metal “see” much more heat and get much more curing of the powder coating than the thicker metal will.
The metal temp statement is used to help equivalent these two situations, so that the coater has an idea of how long to leave parts in the oven no matter what type or how thick the metal is they are putting in the oven.
Given this information, it obviously becomes absolutely important for the powder user to know their oven:
- How long does it take to get ½ “ steel up to temperature? Sheet metal?
- Are the temperature probes in the oven working properly?
- Is the line speed correct? The line speed will of course determine oven dwell time,
- Are there any dead spots in oven that will change the cure on the parts?
- How much heat is being lost on ramp up into the oven and on the exit?
This data, and other data on the oven and the whole production line can have a very substantial effect on the finished powder coating and the durability of the powder coated parts.
How are these questions answered? Many questions, such as those noted above on whether the temperature probes working, are simple maintenance issues. Line speed can be determined manually using a timer.
The most difficult part for a powder user to get to know their oven is determining ramp temperatures, fullness of cure given var-ying temperature through the oven, determination of dead spots, etc. These can only be determined when the oven is running, usually loaded with parts. The only real way to determine this information with the oven working is by using an oven recorder.
An oven recorder can measure dead spots, and given information on quality and fullness of cure. Erie Powder offers a free service for our customers where we can run a data recorder through an oven and get this information to the coater.
Contributing to this Newsletter
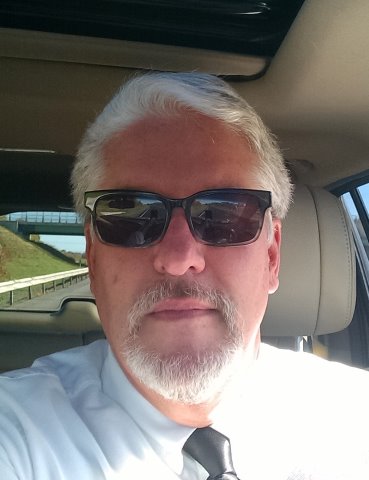
Dan Magruder is sales manager at EPC covering the eastern USA. Dan has extensive experience in sales of powder coating, and previously gained much experience through running a powder coating job shop.
Phone: 518-478-1456
Email: dmagruder@eriepowder.com
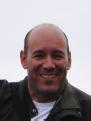
Brian Coutts is President and founder of Erie Powder Coatings EPC. Brian is a chemical engineer, Queen’s University in Kingston and is a proud father of three .
Phone: 905-957-4086
Email: bcoutts@eriepowder.com